Work Order Management Software
Key Benefits
- Assured timely production
- Instant fixing of errors in machines
- Enhanced safety of workers
- Environmental sustainability improved
- Offline access extended
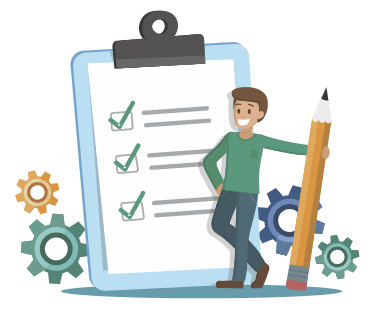
Work Request
Key Benefits
No cadre to raise the
issue
Helps to improve the
workflow
Enrichment in customer
satisfaction
Timely and immediate issue resolvement
Project Handling
Key Benefits
On spot complaint
raised
Timely accomplishment of
project
Keep tracking on project
function
Keep tracking on project
cost
Remote Handling
Key Benefits
Zero
paperwork
Integrity enabled
remotely
Shift response to machine
issues
Timely scheduling of maintenance activities
Mobile App View - Work Order
Where it includes the following details:
Vendor Name
The name of the vendor who supplied and taken the charge to handle product maintenance and issues whenever required.
Work order-id
A separate and unique work order id will be generated to all the machines and equipment exist in the plant to undergo maintenance or bug fixing process whenever required.
Order Raised
Denotes the date on which the work order got raised by the concerned equipment or machine handler. It can also be raised by the senior staff based on protocol.
Due Date
The final deadline within which the assigned task for maintenance or repair needs to be fixed by the concerned technician of the vendor side.
Location
Helps the technician to reach the exact spot of issue prevalence by tracking the locality of the equipment of machine present.
Requirement/Description
States the exact need of the equipment or machine in terms of maintenance or issue handling that comes out in a completely detailed format, explains what needs to be done? And is the persisting issue?
maintenance and issue fixing activity.
Adding Work Order
provide high clarity to the maintenance team.
Title
Denoting the issue in a word or three, more like a subject
of the mail
Department
Mentioning the department under which asset gets operated; it helps to find the asset easily.
Image
Upload the image of the concerned asset to be scheduled under maintenance or repaired, it happens in the mobile app that stores images in separate section.
Repeat Schedule
The mobile app asks out for repeat scheduling of task if in case the machine undergoes maintenance and the concerned user needs to select the repeat mode based on the demand.
Category
Denotes the category under which the specific equipment or machine falls under.
Asset Name
Clearly mention the name of the asset to make sure the right one is treated.
Priority
The priority in handling the particular equipment or machine is categorized as none, low, medium, and high based on the urgency level.
Worker
It includes the specific details of the employee/worker(s) who handles the particular asset.
Signature
Of course a digital signature provided by the authorized supervisor or responsible official who initiates the task of assigning the repair or maintenance activity of the asset.
Part Details
Specifies the entire details of the parts that include their make, year of manufacture, utility etc.