Preventive maintenance is an essential component of asset management, leading to increased equipment lifespan, decreased unplanned downtime, and, consequently, lower long-term maintenance costs.
In this comprehensive blog, we will look at what preventive maintenance is and what it entails, why it is necessary, what its benefits and drawbacks are, how to build a preventive maintenance strategy, and how to outline a schedule.
Quick Summary on Topics Covered
- What is preventive maintenance?
- Types of preventive maintenance
- Applications: when to use or not to use
- The importance of preventive maintenance
- How to create a maintenance plan step-by-step?
- How to outline a creative maintenance schedule?
- Automation of preventive maintenance work order
- Plan assessment and review
- Advantages and disadvantages of preventive maintenance
What is Preventive Maintenance?
Preventive maintenance entails measures that avoid breakdowns and reduce the likelihood of an asset failing. That is, it is a form of scheduled maintenance that is carried out even though a piece of equipment is still operational.
It can be as straightforward as cleaning HVAC filters or testing centrifugal pump bearings, but it also requires more nuanced inspection plans, tuning and/or gauging plans, gas leak monitoring, and other cyclic revisions.
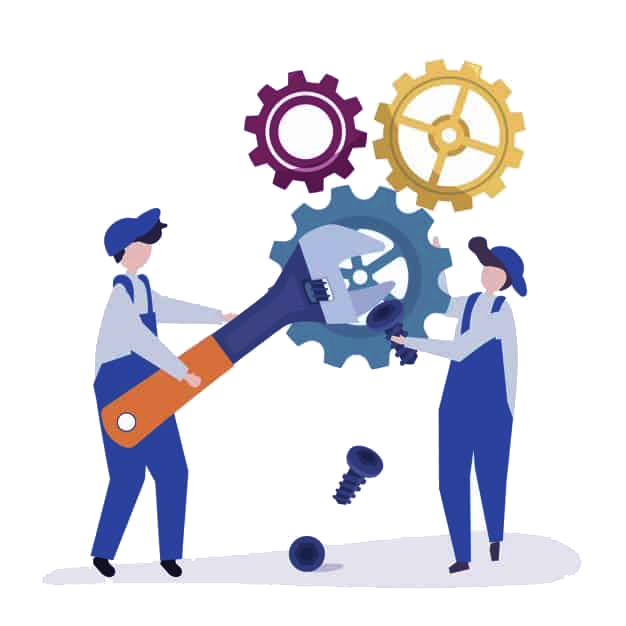
Types of Preventive Maintenance
In general, there are two types of preventive maintenance:
Time-based: Periodic evaluations are carried out at predetermined intervals, independent of asset use.
Usage-based: Based on the assets’ real use.
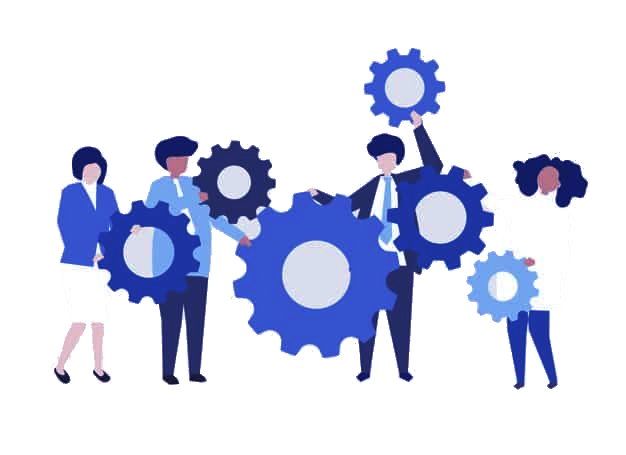
Applications of Preventive Maintenance
Under what circumstances can a preventive maintenance approach be used? In what situations is it best to take a strictly reactive approach? Taking the above-mentioned forms into consideration, let’s look at the circumstances in which this technique is suggested.
When NOT to use preventive maintenance
Let’s start by getting rid of any properties that can’t be used for this technique. If preventive maintenance is dependent on timing, equipment that fails at random, such as a blown lamp, bells, power sensors, or clogged flushes, is immediately omitted.
Preventive repair is usually not the safest choice if it is not feasible to create a standard for an asset’s breakdowns.
When to use preventive maintenance
On the other hand, there are properties whose loss rate increases over time and use. There is a trend in these situations – we will plan repairs by using statistics regarding the planned operation of the equipment and the manufacturer’s advice.
That being said, scheduled maintenance enables one to:
- Extend the life of the asset in question
- Maintain efficiency over time.
We then conclude that preventive repairs should be extended to properties that are critical to the company’s daily service, as well as assets of higher importance whose restoration or removal is more costly than routine preventive operations.
Excessive preventive maintenance, as well as its extension to properties of low value or priority, can result in excessive costs for the downtime avoided.
Why Is Preventive Maintenance So Important?
As previously said, preventive maintenance raises asset lifespan and the percentage of expected maintenance. However, this is not the only reason to engage in preventive maintenance. Finally, preventive maintenance is an important factor in keeping the consumers happy.
- Lowering downtime and raising the effectiveness
- Increasing equipment durability
- Lowering reactive maintenance costs
- Increasing protection
- Increasing comfort
Can you imagine going to repairs without air conditioning in the middle of summer? There are some things we wouldn’t wish on our worst enemy.
How to Create a Preventive Maintenance Plan Step-By-Step?
Preventive maintenance has undeniable advantages. How, exactly? Where do I begin? How do you build and carry out a preventive maintenance plan? Get yourself at ease, and we have the solutions.
The first step in putting a preventive maintenance policy in place is to create a schedule. Both job orders must be clearly established, taking into account products, components, labor requirements, and even the hiring of specialized outside providers. The procedure is divided into five steps:
- 1. Establishing objectives.
- 2. Create an inventory of your assets.
- 3. Determine your goals.
- 4. Developing key performance indicators (KPIs) for the maintenance schedule.
- 5. Evaluate and develop the proposal
We highly advise you to read our professional advice on how to build a preventive maintenance plan as soon as possible in order to bring this into action.
How to Outline a Creative Maintenance Schedule?
Following the creation of your schedule, you must determine dates, timetables, and teams. In a nutshell, it’s a timetable for preventive care or a job plan. This work can also be broken down into five steps:
- 1. Determine labor productivity.
- 2. Examine the backlog of repair tasks.
- 3. Modify the timetable in accordance with the maintenance plan.
- 4. Be prepared for surprises.
- 5. Arrange the work instructions
Preventive Maintenance Work Orders Automation
One of the most difficult aspects of creating a maintenance schedule is mapping properties and cross-referencing them with suggested repairs or inspections. It is almost difficult to organize the entire inventory in infrastructures with a vast amount of properties. Fortunately, most preventive repair job orders may be automated using maintenance management tools (CMMS).
A CMMS helps you to index your assets as well as link them with details such as category, brand, equipment type, serial number, position, supplier, the technician in charge, user manuals, including previous intervention dates.
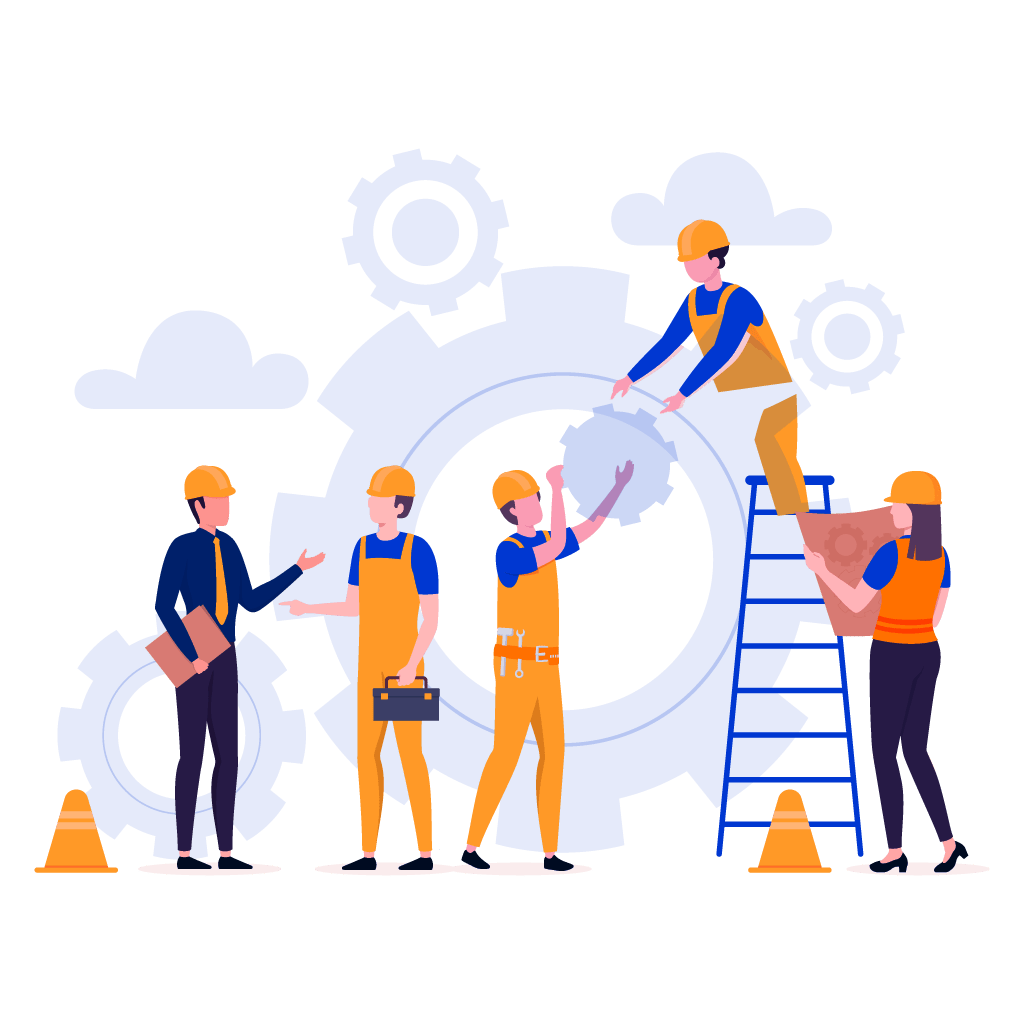
Scheduling preventive maintenance tasks with a CMMS
The use of repair tools simplifies the process of developing proactive maintenance plans for various pieces of equipment.
You should set constraints for creating interventions depending on use in addition to being able to automatically plan work orders that only focus on the passage of time.
Tracking the plan in real-time
Another benefit of using a CMMS for the administration of proactive maintenance task orders is the real-time reporting of plans. The app analyses the data and automatically measures the key KPIs, allowing you to check and adjust the plans at any time.
You should set constraints for creating interventions depending on use in addition to being able to automatically plan work orders that only focus on the passage of time.
Assessment and Review of Preventive Maintenance Plan
There are certain benchmarks and targets you should always be mindful of, regardless of the type of assets you manage or the particular KPIs you have specified for your business. We recall the preventive maintenance golden rules:
1. Preventive maintenance compliance
It reflects the percentage of preventive maintenance done during the specified time period, which must be at least 90%. Find out all on calculating preventive maintenance compliance.
2. Scheduled maintenance critical percentage
It should be as close to one hundred percent as possible.
3. 80/20 ratio for scheduled and non-scheduled maintenance
At least 80% of repair hours should be spent on preventive work orders. Just 20% (maximum!) of maintenance time must be spent on reactive task orders; preferably, 85 percent of maintenance should be planned.
4. The 10% margin rule
With a 10% margin, try to finish all job orders ahead of time. That is if you have a job that needs to be completed in 100 days, try to finish it in 90 days (10 days ahead of schedule).
If your performance falls short of your goals, learn how to assess the success of your maintenance plan and what each of these metrics entails.
Make all your facility management process simple with digitalization!
Advantages & Disadvantages of Preventive Maintenance
We shall now look at the benefits and drawbacks of preventive maintenance, both in terms of the internal running of your activities and the effect on the service delivered and customer loyalty.
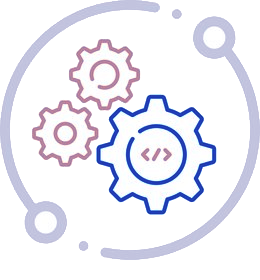
Advantages of preventive maintenance
- Extends equipment lifespan, increasing return on investment
- Prevents unexpected stoppages, improving business operations
- Improves equipment durability, making predictions more realistic
- Predicts (accurately) how you might allocate your resources all through the year
- Saves money
- Increases facility protection
- Meeting consumer deadlines so there are fewer stoppages and it is easier to forecast output
- It offers a smoother customer experience
Disadvantages of preventive maintenance
- It takes more time to plan and inspect
- You might readjust the team's habits and maybe adopt the latest software
- It cannot be used on equipment that occasionally malfunctions
- unwanted maintenance activities; can lead to increased costs if applied to assets of lesser value or priority
- May necessitate further outsourcing maintenance work, compelling you to look for new suppliers
- To make sure that deadlines are achieved, you can sign service level agreements (SLAs) with vendors and partners.
Need more information about iStudio Technologies maintenance management services in India?
Get in touch
Do you want to learn how iStudio Technologies smart Maintenance Management Solutions, which includes end-to-end solution with best technologies usage, which will help you schedule and handle all of your preventive maintenance plans, properties, stock, job orders, and more?